Les 25 ans du Groupe ont été célébrés le 9 juin au Groupama Stadium de Lyon. Imaginé par le cabinet d’architecture Populous (UK) et inauguré en 2016, le troisième plus grand stade de France est fait de béton. L’occasion de faire un point technique sur ce matériau de construction. ????
La structure du Groupama Stadium
120 000 m3 de béton ont été nécessaires pour construire la structure du Groupama Stadium, notamment les 12 noyaux périphériques en béton armé très ferraillés, permettant de répondre aux règles parasismiques du site, sur lesquels s’appuient le gros œuvre portant les gradins préfabriqués en béton armé posés sur des poutres crémaillères et la charpente métallique de la couverture avec sa couverture multicouche. L’enveloppe est constituée de façades conservées en béton brut de décoffrage dans lesquelles s’insèrent de larges parties vitrées.
Le béton, un matériau qui a traversé les siècles
Le terme béton est un terme générique qui définit un matériau obtenu en mélangeant de manière homogène et dans des proportions convenables des granulats (sable et graviers), de l’eau et un liant. Ce liant est souvent du ciment.
Déjà les Romains, qui bâtissaient des édifices importants nécessitant des murs épais, par économie de temps et de matière, utilisaient le béton, dont la qualité a permis de traverser 2 millénaires. Pour exemple, âgée de 1 800 ans, la coupole du Panthéon de Rome, toujours debout et en excellent état, en est l’un des exemples les plus impressionnants. La différence essentielle entre le béton actuel et le béton romain réside dans sa composition : ce dernier contenait de la pouzzolane (cendres volcaniques) et était mélangé directement avec de la chaux aérienne (obtenue à partir de calcaire très pur, tolérance de 5 % maximum d’argile, contrairement à la chaux hydraulique qui peut en contenir jusqu’à 30 %) en pâte et de la chaux vive (non éteinte) à très hautes températures.
Le 20ème siècle, de l’acier, pour augmenter la résistance du béton
Le béton est un matériau très résistant en compression et beaucoup moins résistant en traction (de l’ordre du dixième de sa résistance à la compression). C’est pour pallier cette insuffisance qu’est née l’idée de placer, dans les zones soumises à des efforts de traction, des barres d’acier (armatures) qui, elles, sont très résistantes en traction. Le matériau résultant de l’association du béton et de l’acier dit passif est appelé « béton armé ».
Pour renforcer encore la résistance des structures en béton, les structures peuvent être « précontraintes ». Le premier brevet sur la précontrainte a été déposé en 1928, par Eugène Freyssinet (1879-1962). La précontrainte peut être réalisée par pré-tension ou par post-tension. Dans les 2 cas, il s’agit d’ajouter aux structures en béton des armatures dites « actives », des torons (ensemble de fils tréfilés lisses), dans des câbles et de les tendre à l’aide d’un vérin. Cette technique renforce la compression exercée dans le béton, et donc permet notamment des portées (longueurs d’éléments) plus importantes et l’amélioration de l’étanchéité en évitant les fissures d’origine mécanique. A titre d’exemple, les poutres de l’arche de la Défense sont précontraintes par post-tension (tension exercée après le coulage du béton), ou la digue flottante de Monaco, construite en béton de haute performance et précontraint dans les 3 directions.
La précontrainte par pré-tension (les torons, disposés dans le coffrage aux emplacements voulus, sont tendus préalablement au coulage du béton) est plutôt adaptée en usine de préfabrication (poutrelles du bâtiment, planchers alvéolaires précontraints permettant de franchir des portées de plus de 12 m).
La recherche pour des bétons de plus en plus performants
La recherche dans le domaine de la formulation des bétons depuis 40 ans est très active. Les progrès dans le domaine des adjuvants (produits chimiques incorporés au béton frais pour en améliorer certaines propriétés) et l’utilisation des « ultrafines » (souvent des fumées de silice contribuant à réduire significativement la porosité du béton) ont conduit à une évolution spectaculaire des bétons. Aujourd’hui, on parle de BFUP, des bétons fibrés à ultra hautes performances qui contiennent plus de ciment, un ratio eau/ciment plus bas, des adjuvants superplastifiants et des compositions granulaires spécifiques et des fibres (métalliques ou organiques, à raison de 2 à 3% en volume), en lieu et place de tout ou partie des aciers passifs. Ces BFUP offrent des résistances en compression comprises entre 150 et 250 MPA soit jusqu’à près de 10 fois supérieures à celles des bétons courants. Ils sont en général auto-plaçants et permettent le coulage des pièces à géométrie complexe ou de parois de faible épaisseur.
A titre d’exemples, la couverture du stade Jean Bouin à Paris est une coque tridimensionnelle constituée d’éléments de dalles nervurées triangulaires de grandes dimensions en BFUP, associées à des inclusions en verre, ou encore le MUCEM de Marseille où le BFUP est utilisé pour l’ensemble des structures porteuses périphériques constituées de poteaux arborescents, ainsi que pour la réalisation des résilles habillant les façades et les toitures ainsi que pour les passerelles d’accès.
Dès lors, on voit que parler de béton est complexe, car on peut jouer à la fois sur la composition du mélange constituant le béton ainsi que sur les aciers passifs ou actifs qui renforcent sa résistance.
Pour construire le Groupama Stadium, plus de 20 formules de béton, dont une grande quantité de béton autoplaçants, ont été mises en place.
Le béton autoplaçant (BAP) est un béton très fluide qui se met en place par le seul effet de la gravité (il ne nécessite pas d’être vibré), tout en conservant des propriétés mécaniques identiques à celles des bétons classiques. Ce béton est plus compact, il enrobe mieux les armatures et ne présente pas de défauts dus à une vibration insuffisante, la durabilité de l’ouvrage s’en trouve améliorée.
Le « béton vert », un enjeu pour la planète
Pour terminer, à l’heure actuelle, la production du béton représente 8 % des émissions mondiales de gaz à effets de serre, et les projets de recherche pour un “béton vert”, qui diminuerait son impact environnemental, se multiplient.
Le ciment Portland, composé principalement de clinker (produit par une cuisson à très haute température), est le composant responsable de 85 % des émissions de CO² du béton. En substituant tout ou partie du clinker dans la fabrication du ciment, on obtient déjà aujourd’hui du béton bas carbone à ultra-bas carbone.
La compréhension du fonctionnement du béton romain pourrait également aider à atteindre cet objectif, en permettant de créer un matériau plus résistant, plus léger, et plus durable. Plus écologique en somme !
Catherine Belin-Ventéjol – Directeur Général Polyexpert Construction
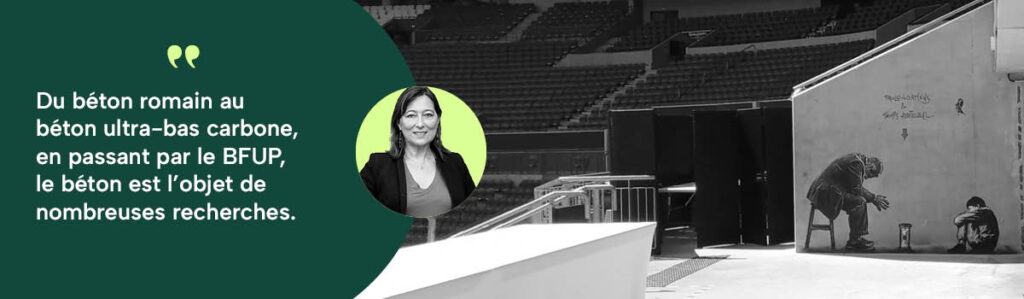
Bio express Catherine Belin-Ventéjol
Polyexpert Construction en Bref
- Directeur Général de Polyexpert Construction et membre du comité exécutif du Groupe Alkera.
- Catherine travaille au Siège social du Groupe.
- Elle est ingénieur ESTP, titulaire d’un MBA IAE, qualifiée CRAC et maman d’une jeune fille de 20 ans et d’un jeune homme de 18 ans.
- Expériences professionnelles : 10 ans à l’APAVE (Bureau de contrôle technique) ; 7 ans chez SOCABAT (Pôle technique de la SMABTP) ; 2 ans chez Hannover re (Réassurance).
- Filiale du Groupe Alkera entièrement dédiée à la Construction.
- Créée en 2010.
- Sa mission : constater les sinistres survenus sur les Bâtiments ou Ouvrages de Travaux Publics, trouver leur(s) cause(s) pour estimer puis réparer les dommages.
- Une équipe de 110 personnes.
- 63 experts dont 35 CRAC ; 44 assistants opérationnels et fonctions support, 2 juristes.
- 15 implantations principales : Bastia, Biarritz, Bordeaux, Cambrai, Clichy (Siège social), Lyon, Marseille, Monaco, Montpellier, Niort, Perpignan, Rennes, Strasbourg, Toulouse, Versailles.
- 11 M € de CA en 2022.
- 11 500 dossiers en 2022.
- Principaux clients : AXA, SMA, COVEA, MAIF, ACS (Prestataire pour comptes), Albingia, Abeille.